White Paper: Five Steps To Save Energy
March 31, 2015
By: Mike Grande
Article originally appeared in the January 2010 edition of Process Heating Magazine
Process optimization is one of the easiest ways to save energy and money on new or existing ovens or drying equipment.
In a heat processing application, the process oven is designed, rated and commissioned for a specific production capacity. This capacity (pounds per hour or pounds per load) typically is a conservative number reflecting worst-case loading at maximum temperature— conditions typically is never encountered in actual production.
This inflated rating makes your oven consume more energy even under normal conditions when the extra capacity is not being used.
By carefully analyzing the product being processed, and then designing and adjusting the equipment to more accurately match that process, you can reduce your energy use and save money, sometimes dramatically.
1. What Are Your Product and Process Requirements?
First, determine your anticipated product loading. For continuous process equipment such as conveyor ovens and web dryers, it is the pounds per hour of product or material being processed through the oven.
For batch ovens, it is the pounds being processed in each batch. Remember to add in the weight of the conveyor belt, baskets, carts, fixtures, etc., that carry the product. Be as accurate as you can and do not put a service factor on your estimates. That should be added later.
Next, calculate the amount (if any) of solvent or water to be evaporated in the oven or dryer. Start by measuring the wet vs. dry weight of a sample of material. The difference in weight represents the evaporated solvent or water.
An alternate method when dealing with a uniformly applied coating is to measure the coating thickness and multiply it by the surface area on which it is applied. By multiplying this by the percentage of solvent that the coating contains, the actual solvent content (per part or per hour) can be determined.
The final step is to multiply by the number of parts per batch (for batch ovens) or parts per hour (for continuous ovens).
No matter what method is used, it is critical that the solvent measurement is done accurately. The solvent load has a drastic impact on the exhaust rate, which has a direct effect on the heat input (and energy use) of the equipment. In many instances, the exhaust system consumes even more energy than heating the product itself.
Solvents are flammable and must be properly exhausted in accordance with National Fire Protection Association (NFPA) Standard 86 to prevent unsafe concentrations from accumulating in the equipment.
In the case of a water-based coating, there are no mandated exhaust requirements. Instead, the exhaust rate should ideally be determined by testing. To test, start at the minimum exhaust setting (using the damper or variable-frequency drive), and perform drying tests with successively greater exhaust rates until the parts dry properly. The key is to exhaust no more air than is necessary.
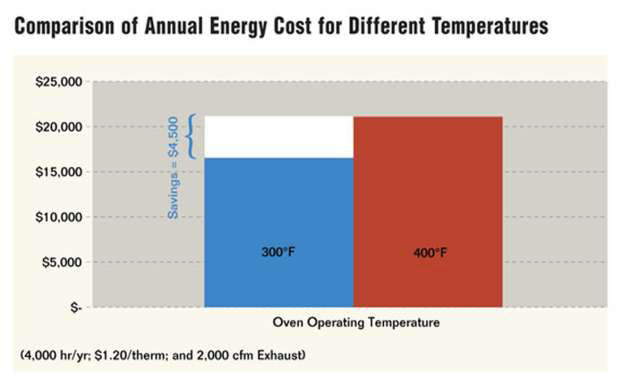
Figure 1. Even a 50 or 100ºF (28 to 56ºC) reduction in operating temperature can potentially save thousands of dollars in annual operating costs.
For gas-fired ovens, additional exhaust is required to remove the products of combustion, which also removes heat from the oven and can result in wasted BTUs.
For gas-fired ovens that utilize excess air burners—and most do—this wasted heat is based on the maximum burner rating regardless of whether it ever operates at its maximum. Therefore, an oven equipped with an oversized burner costs more to operate than an oven with a properly sized burner.
When purchasing a new oven, make sure the burner is sized to match the heat requirements of your process with a reasonable safety factor added.

Figure 2. Reducing the solvent content allows you to reduce the oven exhaust rate, which minimizes energy consumption.
2. What is the Heat Input Required?
Using the product and process data, calculate the heat input required to perform the heating operation for your specific parts, process and coating. Or preferably, choose an oven supplier that can do it for you.
Often, these factors are only roughly (and conservatively) estimated during the proposal stage. But, when the oven is purchased and enters the design stage, the details must be finalized. When this is overlooked, the equipment often is over-designed. It wastes energy and money during operation.
When purchasing an oven that is a standard offering from the manufacturer, make sure these calculations are made. This step can often be ignored or forgotten.
3. Be a Smart Coating Shopper
Before selecting a paint or powder coating, consider not only the cost of the coating itself but its cure temperature.
The temperature can have a large impact on energy consumption (Figure 1). Ask your oven supplier to calculate this because even a 50 or 100°F (28 to 56°C) reduction in operating temperature can potentially save thousands of dollars in annual operating costs.
Consider the solvent content of the paint you are selecting and consider a water-based coating if possible. Reducing the solvent content allows you to reduce the oven exhaust rate, which minimizes energy consumption (Figure 2).
Ask your oven supplier to compare the exhaust rates and operating costs for coatings with different solvent contents. Reducing the solvent content by 30 percent, for example, may allow you to reduce your oven exhaust rate by 20 to 25 percent, resulting in significant energy savings.
When using a solvent-based coating, consider a solvent monitor, also known as an LEL (lower explosive limit) sensor. It will monitor the atmosphere inside the oven and protect against the buildup of potentially flammable solvents, allowing you to reduce the oven exhaust rate by up to 50 percent without causing a safety hazard.
This can drastically reduce your energy use, especially for high solvent applications.
4. Apply A Safety Factor Only Once
Apply a safety factor only after you have calculated the required heat input. A common mistake is to apply a service factor to the solvent load, then add another one to the load weight, and yet another to the maximum operating temperature.
Compounding the problem is that your oven supplier will probably also apply a service factor when calculating the exhaust rate and selecting the burner or electric heaters.
The accumulated effect often is a significantly over-designed system that may be more expensive than necessary to operate.

Figure 3. This wood drying system is most efficient when running at its maximum design capacity of 6,900,000 boards/year. When operating at reduced throughput, the BTU consumed per board is greater than at maximum throughput.
5. Startup and Adjustment
During startup, adjust the equipment as closely as possible to the actual requirements. Do not heat your product longer or hotter than needed.
When adjusting the exhaust system, do not roughly estimate the damper or variable frequency drive settings. Instead, take actual exhaust flow measurements to ensure the oven is exhausting no more than the required air volume. Don’t let all your effort in optimizing the equipment be wasted by haphazard setup.
New Ovens or Existing Equipment
These five steps can be performed on existing equipment as well as new. In fact, some of the greatest energy savings opportunities are found on existing ovens. Because new equipment is not needed, the investment is minimal and the return on investment is usually favorable.
In addition, your state may provide an energy-efficiency rebate (up to 100 percent in Wisconsin, for example) for the cost of a consultant hired to perform the necessary assessment.
Additional rebates (up to 30 percent in Wisconsin) also might be offered for the cost of labor and materials required to make efficiency improvements.
With a few simple steps you can optimize your thermal process to save energy and money, increase your bottom line, and effectively deal with rising energy costs.